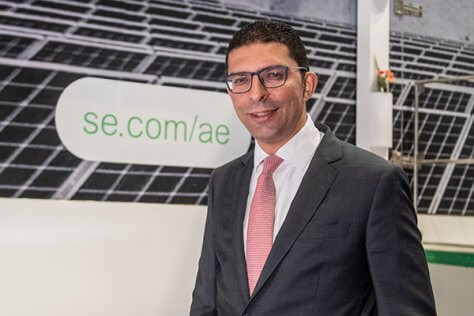
Over the past year, many columns and inches have been given over to the importance of digital in sectors such as retail and the service industry. But I want us to take a step back and look at what is a fundamental part of the global, regional, and national economy. Manufacturing has taken a huge hit this year. Some factories have had to shift production, to help producing medical supplies. Others have had to close down due to safety precautions. And then there’s been the impact on supply chains.
Manufacturing matters to us all. Every society needs a stable, regular supply of goods. And yet we’ve all seen empty shelves in our stores. Manufacturing needs to be more resilient. For many factories, there’s an over-reliance on traditional ways of working, of documenting operational procedures on paper. And when a crisis strikes, these operations cannot adapt.
Speaking to our customers across the region, it’s clear how much they’ve benefited from digitising their manufacturing facilities. By embracing digital as a way of working, manufacturers have looked to improve their efficiency, make their operations faster and more sustainable. What they’ve appreciated the most this year is how much more resilient their operations have become.
Manufacturers across the globe are digitising their operations to improve factory design, engineering, operations and maintenance. These companies are investing in digitisation to achieve one common goal: increased productivity. Digital transformation brings sweeping benefits to manufacturing. But seeing that transformation through from start to finish can be tricky.
Leading industrial organisations pursue digital transformation for five primary reasons:
- Correction of operational inefficiencies
- Creation of competitive advantage
- Elimination of inefficient processes
- Establishment of a stable IT/OT architecture base
- Creation of new customer value and new business models
The current wave of industrial transformation is about connecting and enhancing existing systems to achieve a business benefit. For this reason, connectivity platforms such as EcoStruxure provide an open framework for enabling new ways to solve business-driven challenges across industries.
We’ve learned how effective this is through our own experience. We recently transformed one of the UAE’s fastest growing dairy farm into a modern, smart establishment. The dairy farm’s operations have been digitised through a combination of software and hardware provided by Schneider Electric. The software platform provides the facility team with vital data and analytics for production processes, allowing them to improve output, as well as the ability to track and trace produce.
Using an Internet-of-Things approach and connecting all the plant’s equipment has increased equipment efficiency and reduced downtime. The result is a smart manufacturing model, and one of the most productive dairy plants in the UAE.
Converging the IT and OT space needs domain expertise to drive it – someone who understands the process in the factory. As well as providing digital solutions, Schneider Electric also provides expertise on both the automation and software sides. People who know the industry and our customers’ processes as well as the technology.
The next practice is the end-to-end integration of industrial and engineering software, to help bring the digital plant to life. The digital thread, which connects the digital twin with real time data produces a holistic and up-to-date view of an asset which may as well be the complete plant across its lifecycle.
We supplied a range of electrical solutions that will be installed at Sharjah’s first waste-to-energy plant, the first commercial waste to energy facility in the Middle East. Our technology will optimise the energy efficiency of the plant’s electrical network, reducing the plant’s carbon footprint, and will also ensure that the plant is Internet of Things ready thanks to the equipment’s in-built sensors.
Such integration helps connect people, assets, and operations to boost productivity and profitability. And using technology that is built for the future, this model ensures manufacturers get the most out of their industrial operation over its lifetime.
The current wave of industrial transformation is about connecting and enhancing existing systems to achieve a business benefit. For this reason, connectivity platforms such as EcoStruxure provide an open framework for enabling new ways to solve business-driven challenges across industries.
The question is, are you ready to accelerate the pace of your industrial transformation?