Karen Ravindranath, director, WebNMS – IoT division of Zoho Corp, discusses how IoT can accelerate remote asset management and business continuity strategies.
“There are decades where nothing happens, and there are weeks where decades happen.” — Vladimir Lenin.
COVID -19 has led us all to humanity’s biggest crisis. Although the viral threat has posed several impediments, the world is combating with courage and practical approach towards weeding out the infection. Similarly, the businesses around the world are feeling the pinch due to the current situation. They are finding ways to combat the temporary slow down and new ways to handle the crisis.
According to PwC, about 80 percent of manufacturers expect that the pandemic will have a financial impact on their business. The study was done by the National Association of Manufacturers (NAM) recently. That is significantly higher than the 48 percent of cross-industry companies that are concerned about the same impact, which is based on CFO responses to a study by PwC.
During such sudden and unforeseen crisis when people’s safety is a priority, its technology that comes to aid and ensures ‘Total Business Continuity’. According to PwC, manufacturers are now reconsidering their automation and contingency plans to face business during such times of adversity.
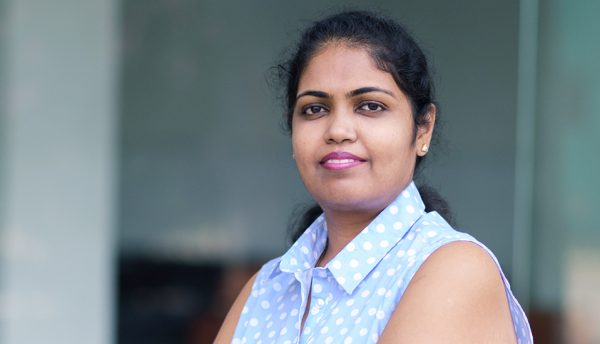
The Internet of Things technology can help build powerful tools that can empower automation and remote management using the internet to stay connected to the IT, non-IT assets and business operations which are of critical importance than ever now.
In the current scenario of restricted people’s movements, supply chain encumbrances, and transportation disruptions, businesses are challenged with operations crisis, especially those that require humans to be on-site. This is where IoT solutions can help solve the challenge by handling repeated tasks and using data to empower human intelligence from anywhere, anytime without actually having to be on-site.
The data from IoT solutions can play a huge role in holding together the business and managing the situation proactively for the operations and business leaders. It can also help to minimise losses that could be incurred due to unnecessary operations of assets and greatly empower the staff to stay updated on the operational whereabouts without having to actually be on-site.
Envisioning remote site/asset management to handle crisis: Why does a business need it?
Today, the word ‘remote’ has far more impetus on it than any time in the past. With social distancing and travel restrictions in place, how can the managers, administration heads and business leaders have access to their sites operating at multiple locations? The question that has been on everyone’s mind ever since things started getting crucial. It is also highly critical for day to day technicians to stay updated on the remote sites they have been assigned to and be able to access data despite the physical distancing.
Again, fragmented communication could pose a huge hassle during such a crisis. According to Darron Gifford – An automotive industry consultant, ‘An automaker may know who’s producing its electronic assemblies and circuit boards, but have little knowledge about second-tier suppliers manufacturing their ingredients’. This is due to fragmented communication and lack of transparency in the supply chain.
IoT powered remote management help connect these dots and keep the businesses updated for crisis planning and management.
COVID 19 has given us good enough reasons for businesses to understand the importance of having access to information of fixed and moving physical assets from from the comfort of home, NOC or any place that isn’t close to the source of data itself.
There are large corporations and facilities which have a million dollars worth assets located at multiple sites and might need them to be up and running despite such challenges posed by a pandemic. For instance, let’s take huge telecom companies which require their cell towers to be operational at 100 percent uptime and efficiency now. IoT powered solution can help centralise these operations, access the remote sites through continuous and proactive monitoring, helping teams schedule maintenance on demand and keep the managers on vigil from the comfort of their homes. Similarly there is a considerably different load patter on the grid with commercial establishments shut down however the domestic load is higher than ever, because of the people staying at home. IoT remote power grid monitoring applications help in proactive monitoring, instant anomaly reporting and keeping teams prepared in case of some discrepancy. In fact this is a perfect example of how IoT can play a huge role in gearing up cities to become smart and prepared for any unprecedented situation.
Furthermore ensuring safety and security of staff, it can also prove to be cost effective because periodic maintenance drill can now become maintenance on-demand. Similarly proactive monitoring can help identify breakage or shutdown, this can help avoid unnecessary downtime and losses due to it.
For field service personnel who are operating on thin teams, knowing which assets need proactive attention and which assets don’t, can mean the difference between maintaining optimal SLAs to having a crisis on their hands at this critical time as this .
Business continuity and digital transformation
Businesses need to stay sustainable; despite the health crisis, organisations are finding ways to empower their staff through applications that can help them work from the comfort of their homes and also cater to customers’ demands even when the operations have gotten a bit challenging.
As far as traditional Business Continuity is concerned most organisations have their IT operations in place and are often equipped for remote support/working. All the staff are given essentials like e-mail ids, laptops and they use cloud business suites to stay connected to their colleagues as well as customers. The question arises for non- IT operations teams; how are they able to manage operations that need humans to be present on-site? How are they combating the challenge of restricted movements? How is the team staying updated on asset health that is located miles away?
Purpose built IoT Remote Management solutions can be of great help to business continuity needs of operations teams. Industries such as logistics for FMCG and essential goods during this period are challenged with limited manpower as well as lack of supply chain cohesiveness. Fortunately these industries can leverage connected data and insights coming in from the various IoT data points. With connected data, the supervisors and managers in charge can proactively plan their operations with limited resources and also be prepared for supply chain contingencies. In the case of limited movements and cut of supply from any specific region, the data connected applications can help with managers stay proactive, procure goods from other sources and also stay informed in case of sudden discrepancies during the movement of supplies from one region to another. All this and more due to staying connected using continuous data monitoring.
Also, in the case of maintaining large immovable assets such as HVAC, DGs and other high capital machinery, how can facilities and admin teams stay proactive in maintaining asset life cycle and also engage in proactive maintenance activities while keeping the health and safety of their staff as a priority? This is where data intelligence can have a powerful impact on human intelligence! Remote site applications driven by the Internet of Things can help teams scrap off the guesswork and move their operations to digital and advanced formats so that technicians can automate the usual operations and step out only when it is absolutely required. This can prove to be a huge backbone for business continuity and crisis management for the organisation at large and help make strategic moves that could benefit the business, later.
This applies to operations managers at manufacturing units, facility managers at large buildings like airports and hospitals etc can stay updated on their remote operations even during this lock down period, because of the leverage IoT has got to offer from remote sites.
As white collared workers stay connected to work and customers from the comfort of their homes, IoT data and applications can empower field staff and blue collared technicians to also leverage data to stay connected and informed without having to step out. IoT along with AI, automation and remote management can be a great tool to empower human intelligence and business operations with or without crisis!